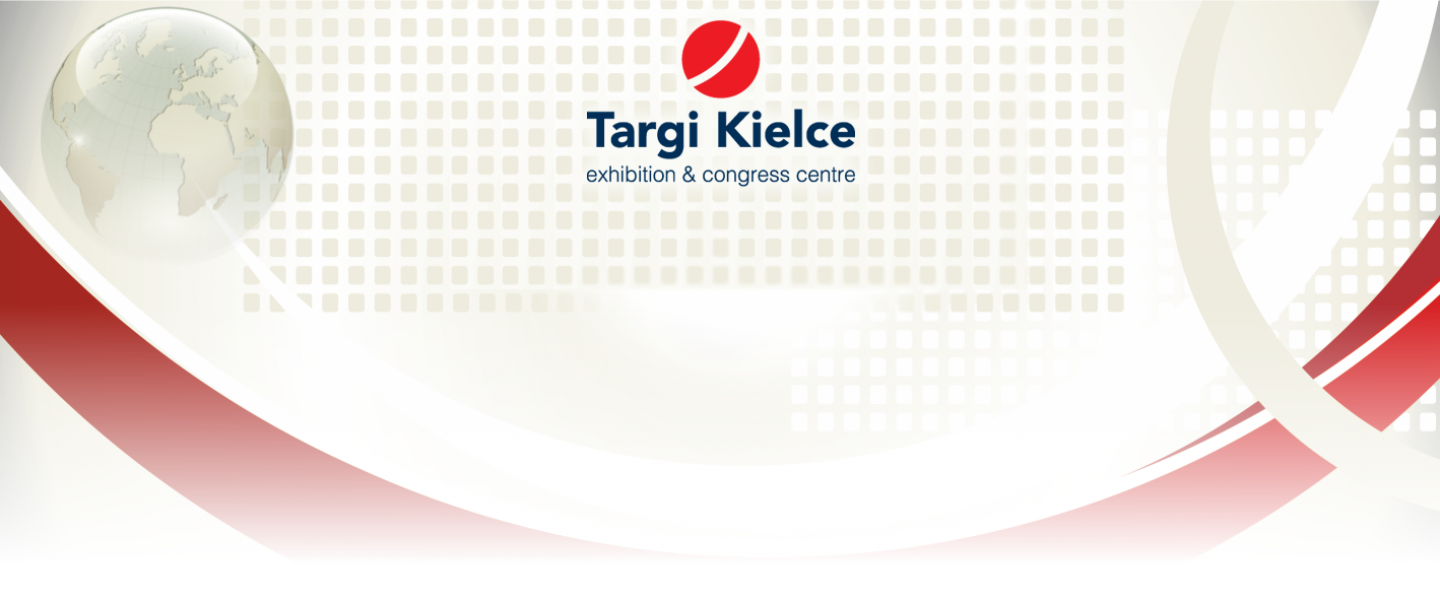
24.04.2019
More and more comfortable and safe cars require perfect, mire refined plastics. The automotive industry drives the development of polymers. This is one of the themes largely discussed at the PLASTPOL Expo
"Anti Squeak" by Albis
The German Albis Plastic rolled out its "Alcom MS Anti Squeak". The compound has been developed specifically for automotive and consumer electronics industries. Anti squeak potential application areas range from plastic components and housings in truck interiors through consumer electronics casings. ABS-, PC-, or PC+-based composite materials offer improved “stick-slip” behaviour which reduces the risk of unwanted noise when in contact with other casing materials. Thus, the company claims it prevents the creaking and cracking noises that consumers associate with lower quality products. The newly developed was put into Ziegler test (VDA 230-206). The results were quite encouraging and demonstrated no significant impact on the new compound’s mechanical and rheological properties. All materials were evaluated in terms of lacquerability and low emissions in order for them to be used in vehicle interiors.
New Solvay developments - PPS and PA6.6
Solvay SA has recently introduced the new, polifenylenosulfid and 6.6 polyamide plastics grades from recycling. The three new RPS PTY brands are designed for extruded automotive parts. According to the manufacturer, the new materials offer certain, highly desirable in properties. Inherent flexibility makes the new grades a perfect choice in making pipes and pipelines. Products made of the new materials can be bent to adapt to the under the hood locations. This is also a perfect choice for flexible, lightweight cooling ducts, brackets and connectors. In these applications, they can compete with polyamide 11, polyamide 12 and metal .
The recyclate-based Technyl 4earth series polyamide from Solvay are already used by the German Karcher, the producer of high-pressure cleaning equipment. To date, Karcher has produced more than 1 million lances with 30% reinforced glass fibre and recycled polyamide 6.6.
Solvay also considers starting a second installation for 4earth polyamide obtained from recycled air bags made of polyamide 6.6. Originally these were made of the 6.6 Solvay Polyamide original grades.
Solvay has recently focused on other polyamide types for automotive market - Technyl and Technyl Star for e-mobility. This product class includes seven grades for electric vehicles cooling systems, sensors and connectors as well as high power chargers.
The new PA 66 for automotive applications
The polyamide 66 manufacturer - the Ascend Performance Materials developed the plastic offered in the market under the trade name of "Vydyne R433H". Vydyne R433H, is designed to reinforce down-gauged steel and aluminium used in vehicle body in white (BIW) structures, BIW structures account for 50% of the vehicle weight, thus the new plastic material helps reduce weight without comprimising safety or comfort.
Vydyne R433H has improved energy absorption properties compared to traditional glass-filled PA66, offers noise, vibration and harshness (NVH) reduction and increased impact energy absorbing capability in case of a car collision. According to Ascend, the new material help car manufacturers reduce vehicle weight and increase productivity.
The new Polyurethane Durethan Performance Polyamid Series by LANXESS.
There is always-increasing need for improved, long-term resistance to cyclic mechanical loads also known as fatigue strength. Plastic parts under the hood need to demonstrate especially high fatigue service life. Thus LANXESS has developed a new polyamide 6 series under the name Durethan Performance. The new grades are several times more resistant to material fatigue caused by pulsating loads compared to standard products of the same fibreglass content. The Thermally stabilized grades - Durethan BKV30PH2.0, BKV35PH2.0 and BKV40PH2.0 with a glass fibre content of 30%, 35% and 40% are the first products in the series, now it also includes the modified, impact-resistant Durethan BKV130P with a 30% glass fibre content. The letter "P" in the product name stands for "Performance".
With these new products LANXESS responds to the demand for automotive industry materials used in air intake systems, oil filter modules and parking brakes - says the tworzywa.pl portal’s expert. The material offers a huge applications potential also in power enclosures and structural of parts tools such as drills and grinders. When it comes to the furniture industry, the modified impact-resistant material grades may be for example used to locks parts.
In addition to dynamic properties, the mechanical static properties profile of new construction materials has also been improved and thus offer a higher tensile strength compared to standard products with the same fibreglass content. The mechanical properties make the polyamide 6 based Durethan Performance materials an attractive alternative to the polyamide 66 grades whose price has increased in recent years. this material swap may be seamless, without the need to increase the fibreglass content which may require coping with materials higher density and hence higher mass.
The LANXESS Group plans to expand the Durethan Performance products range further - the two materials 50% and 60% fibreglass grades are to be rolled out soon. The materials offer high strength and rigidity which makes them particularly well-suited for structural components designed to sustain dynamic loads, e.g. ultra-light components for the automotive industry, such as support elements for electrical and electronic modules.
The LANXESS Group also conducts threshold load tests for cooling systems parts as well as tests for pressure-change and combustion-resistance tests in the intake manifold.
Recommended news